P-NET in General
The P-NET Fieldbus is designed to connect distributed process components like process computers, intelligent sensors, actuators, I/O modules, field and central controllers, PLC’s etc., via a common two wire cable.
This replaces traditional wiring, where a great many cables are involved.
Process data (e.g. measurement values, valve signals) are transmitted digitally. P-NET is also used for data collection, for configuration of nodes/sensors, and for downloading of programs.
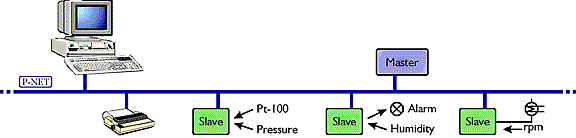
Apart from the usual measurement values and status data, the bus provides a bidirectional exchange of additional information concerning limit values, actuator positioning and feedback signals, fault signals and internal system data.
P-NET can be used to download parameters and programs to modules, which then control the process. The use of intelligent P-NET sensors and actuators also offers much better diagnostic features than with traditional wiring.
Further comparisons with conventional wiring, show that the incorporation of P-NET offers proved advantages when applied to industrial processes.
The result is a simplification of planning and installation, a reduction in the amount and cost of cabling, a reduction in installation and maintenance costs, a reduction in installation errors, leading to a more straightforward future expansion of applications. Instant information about field device faults, and faults in the cable, can be detected automatically by the network protocol.
P-NET applications are characterised by their low cost for a small system. The cost rises linearly with the size of a system.
P-NET is as well suited for small plants, as for large plants having many controllers, sensors, and interface modules. In addition, any such system is always ready for any necessary expansion.
Application Areas
The P-NET Fieldbus has been used for many years, and more than 10.000 applications are now in operation worldwide. Applications range from simple installations with a few I/O points, to very large and complex installations using many thousand I/O points.
P-NET applications are found in the process industry environment and in discrete parts manufacturing plants.
The following typical examples show where P-NET is currently installed and running: Dairies, breweries, environmental control in agriculture, animal feeding systems, asphalt and concrete production, textile industry, milk/oil/fertilizer distribution trucks, quality control systems, power plants, solar power plants, plastic moulding, ship engine control, tank management/alarm systems (approved by German Lloyd, Bureau Veritas, Norske Veritas, Lloyds Register of Shipping), data acquisition, water supply, building automation, fuel management systems, (approved as legal for trade by PTB, NMI, NWML, …).
The typical P-NET application requires response times measured in ms, and a bus length up to one km or more.
The History of P-NET
P-NET was conceived in 1983. The first product using this multi-master Fieldbus was launched in 1984.
The multi-network and multi-port functions were added to the protocol specification in 1986. The first operational P-NET multi-port product was produced in 1987.
The P-NET standard became an open and complete standard in 1989, for adoption worldwide.
Due to an increasing interest in P-NET, the International P-NET User Organization was formed a year later.